Increasing the expected life of assets across all your facilities involves a combination of strategic planning, proactive maintenance, and proper management practices. Here’s a step-by-step approach to help you achieve this goal:
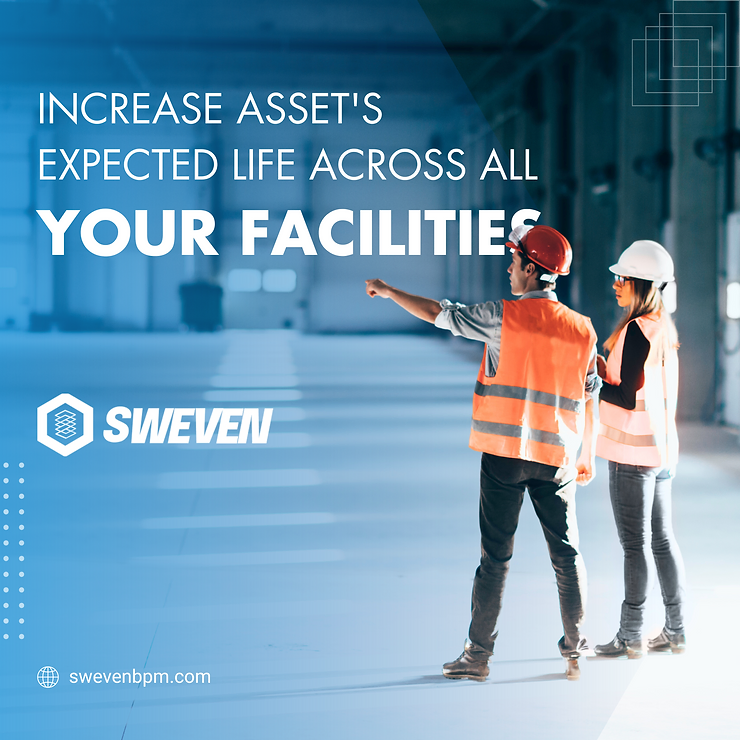
Asset Inventory and Assessment:
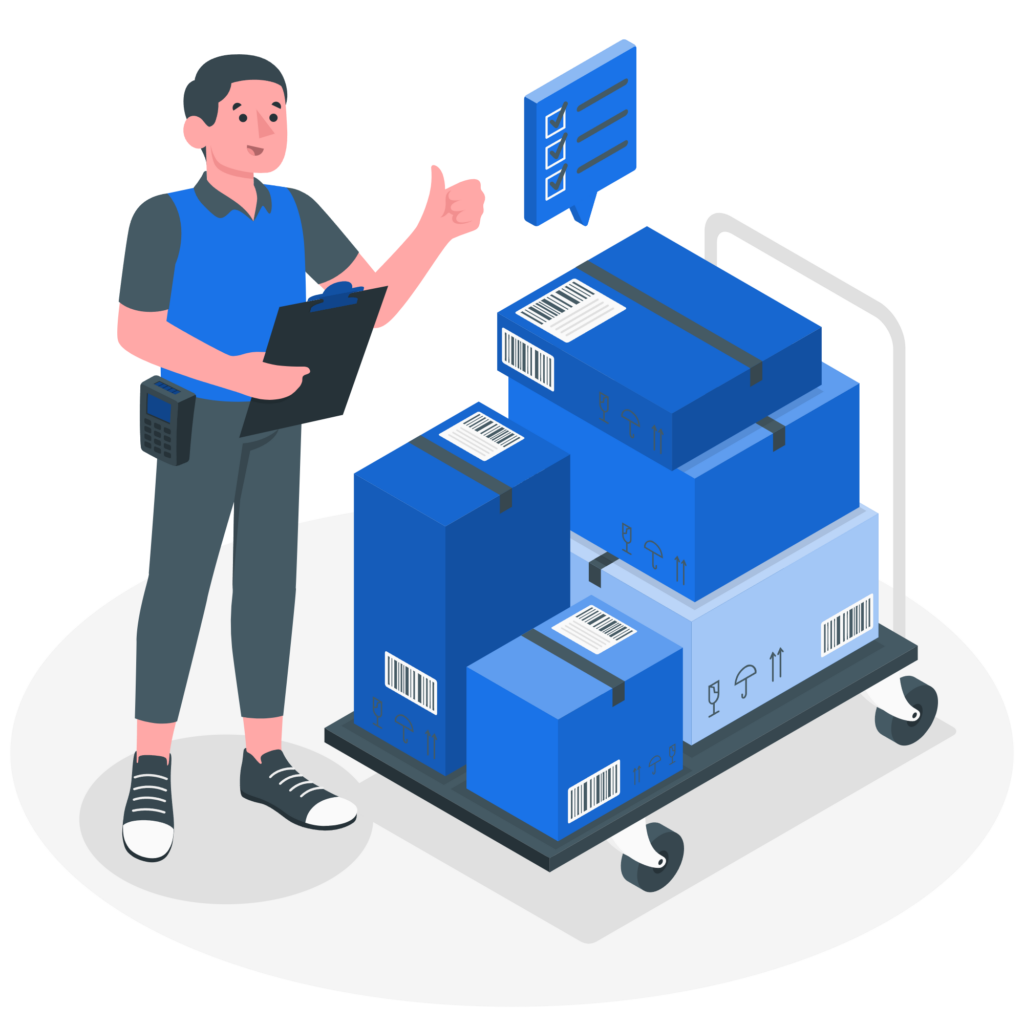
- Begin by creating an inventory of all assets across your facilities. Categorize them based on their type, criticality, and expected lifespan.
- Assess the current condition of each asset to understand its deterioration level and potential areas of improvement.
Strategic Planning:
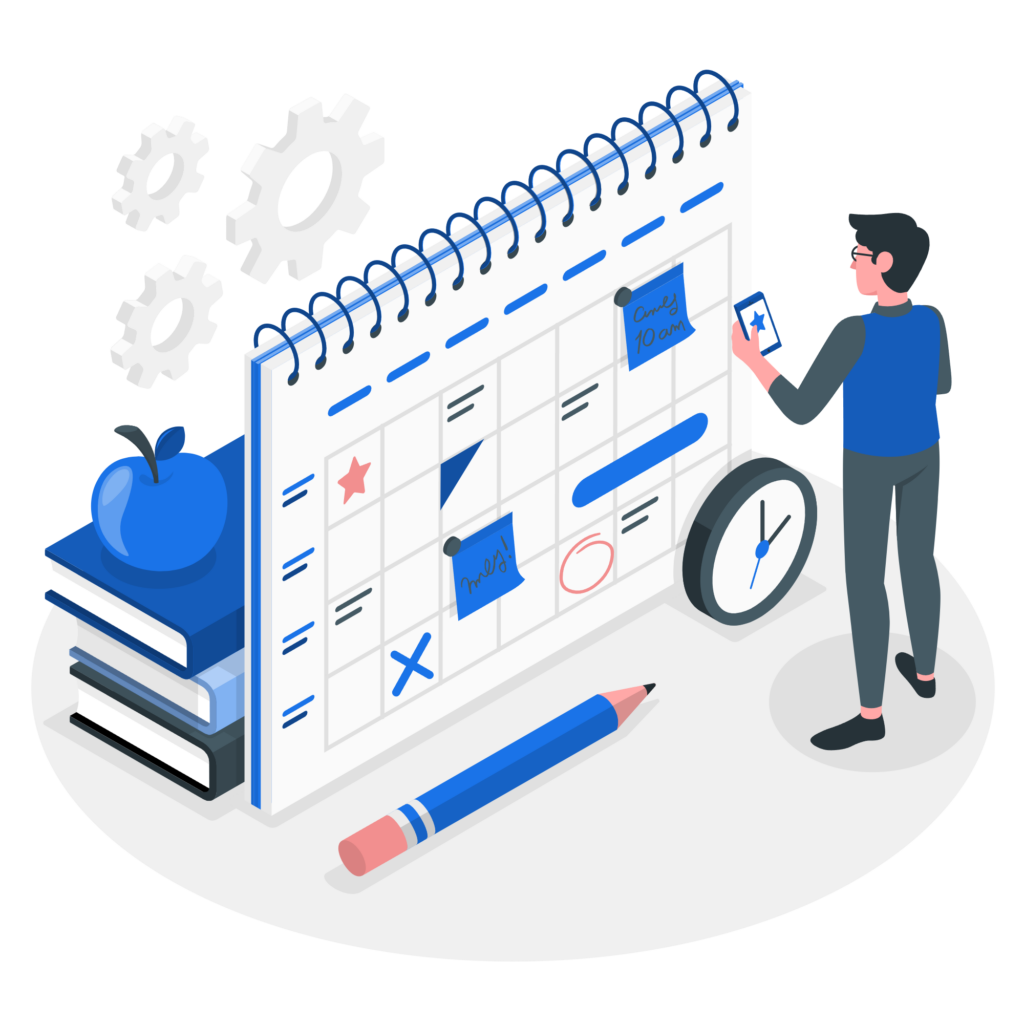
- Develop a comprehensive asset management strategy that outlines your goals, objectives, and key performance indicators (KPIs).
- Prioritize assets based on their criticality to the operations of each facility and the potential impact of their failure.
Lifecycle Analysis:
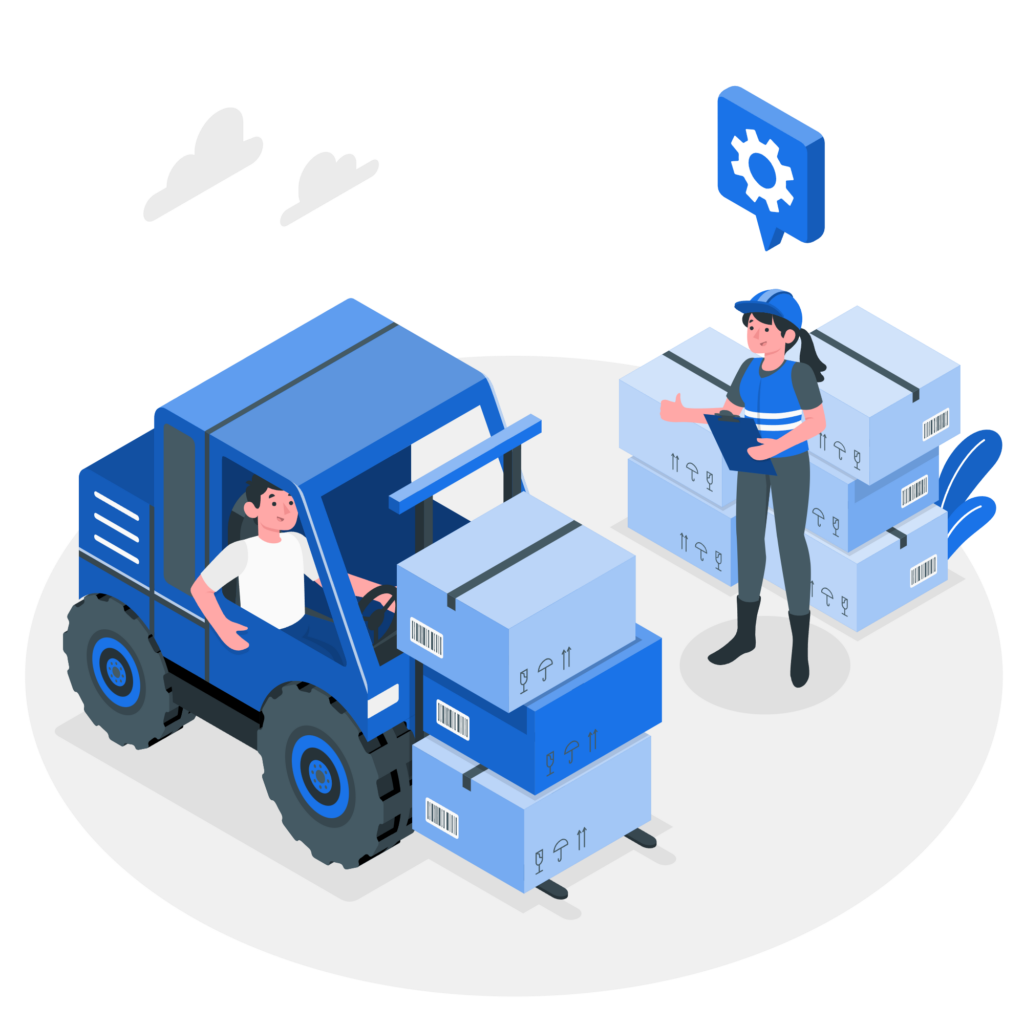
Determine the expected lifecycle of each asset type. This involves understanding how long each asset is designed to function efficiently and when it should be replaced or upgraded.
Maintenance Strategy:

- Implement a proactive maintenance approach, such as predictive and preventive maintenance, to identify and address issues before they cause significant damage.
- Create a maintenance schedule that outlines regular inspections, servicing, and replacements based on the asset’s lifecycle and condition.
Data and Technology:
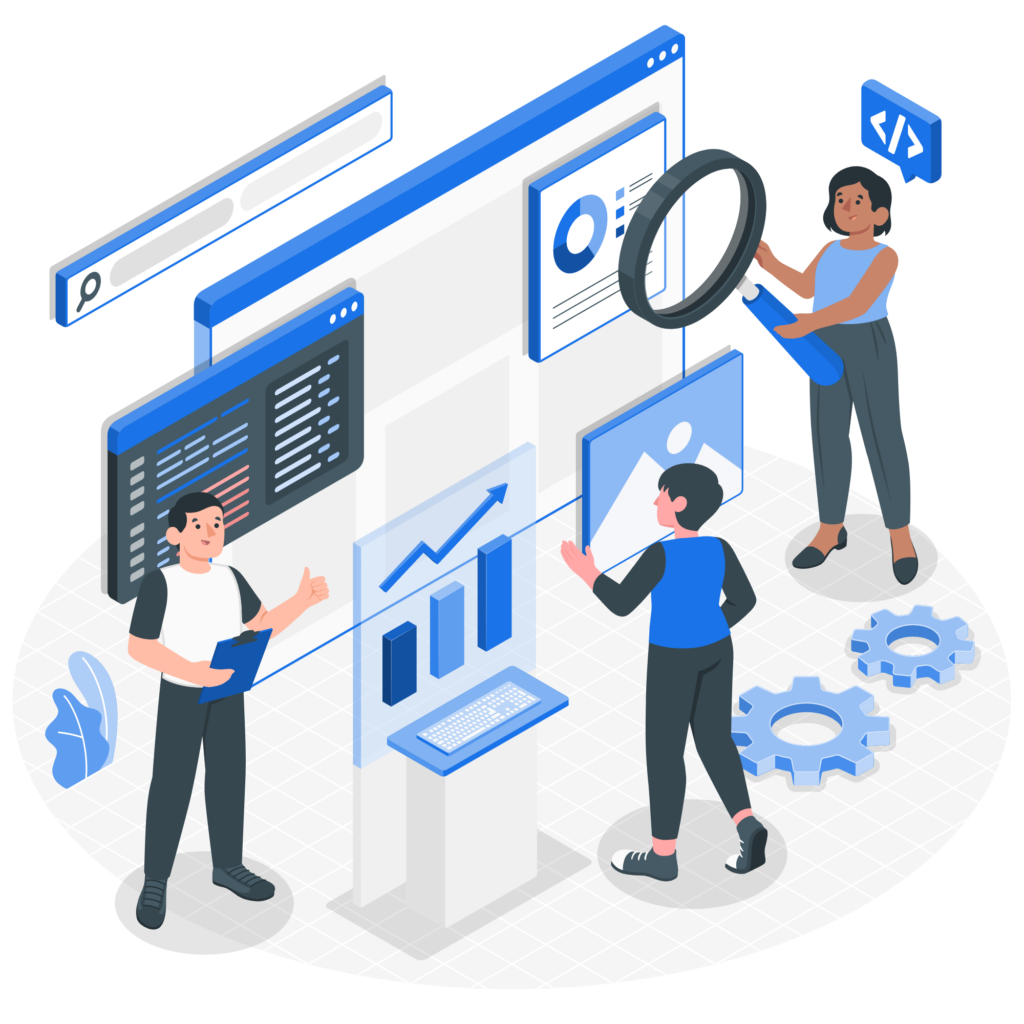
Utilize sensors, IoT devices, and data analytics to monitor asset health in real-time. This data-driven approach can help you detect anomalies and make informed decisions.
Training and Skill Development:
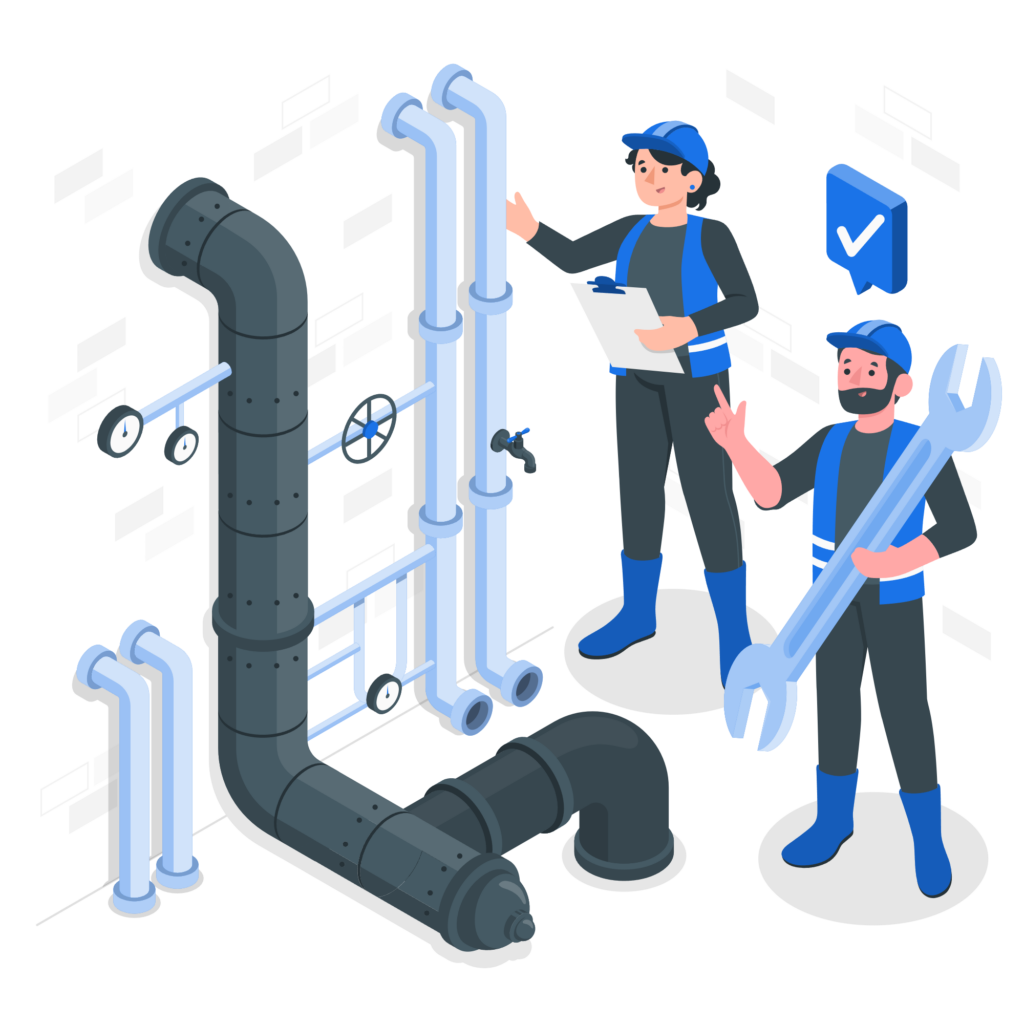
- Train your maintenance teams to use advanced techniques and tools for asset management, maintenance, and repair.
- Foster a culture of continuous learning and improvement within your maintenance workforce.
Supplier and Vendor Collaboration:
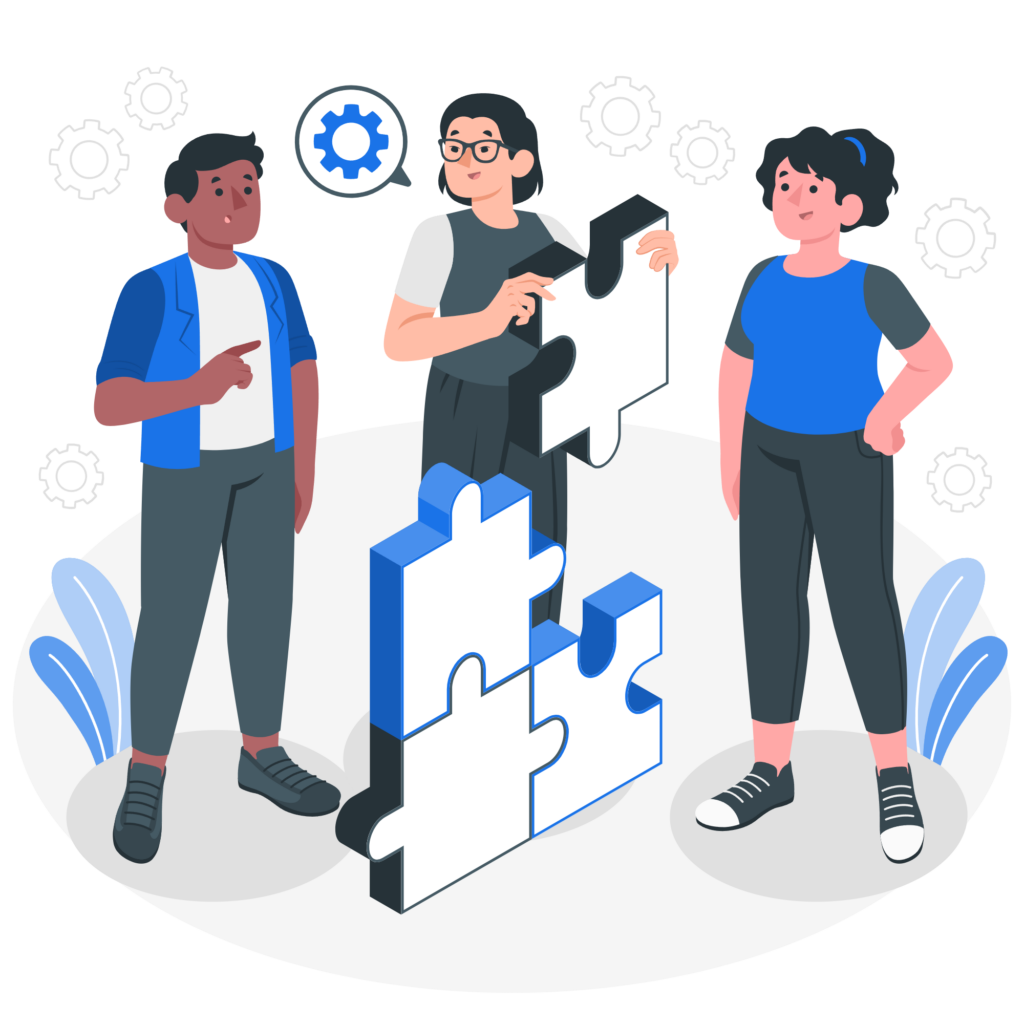
- Engage with suppliers and vendors to ensure that you are using high-quality materials and components in the maintenance and repair of assets.
- Explore extended warranties or service agreements for critical assets to ensure their longevity.
Documentation and Record Keeping:
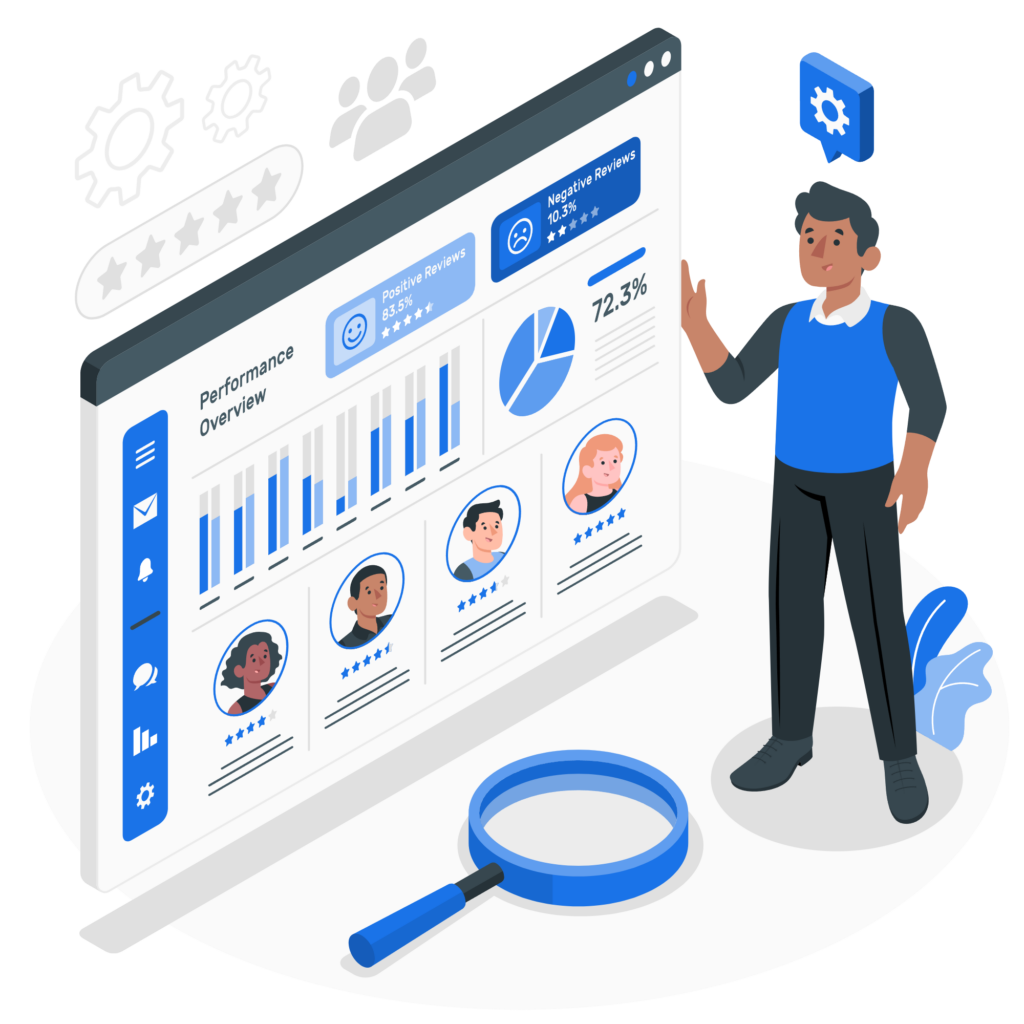
- Maintain accurate records of all maintenance activities, repairs, and replacements for each asset.
- Use a computerized maintenance management system (CMMS) to keep track of asset history and performance.
Optimize Operations:
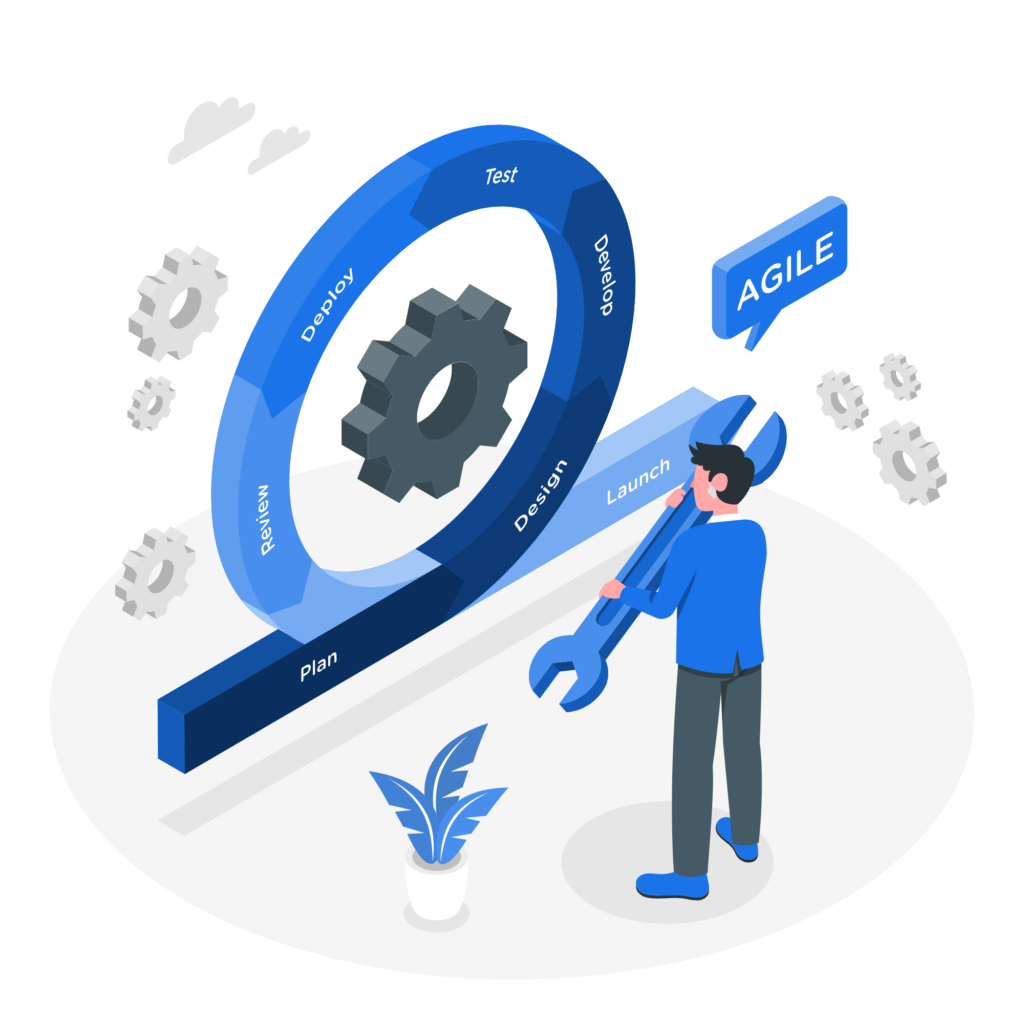
- Ensure that assets are operated within their design parameters to prevent premature wear and tear.
- Implement energy-saving practices that can reduce the stress on assets and extend their lifespan.
Continuous Improvement:
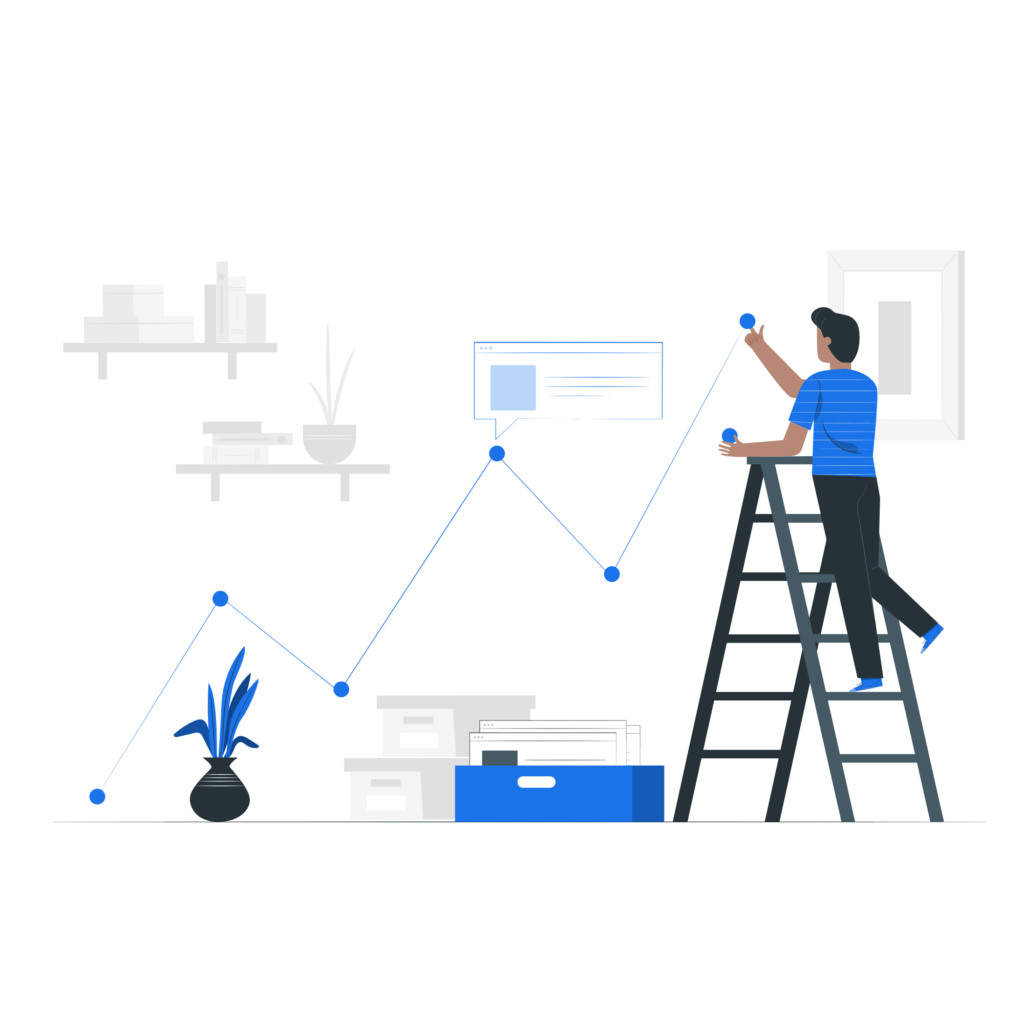
- Regularly review and analyze maintenance data and asset performance metrics.
- Identify trends, patterns, and opportunities for improvement to refine your asset management strategy over time.
Budget Allocation:
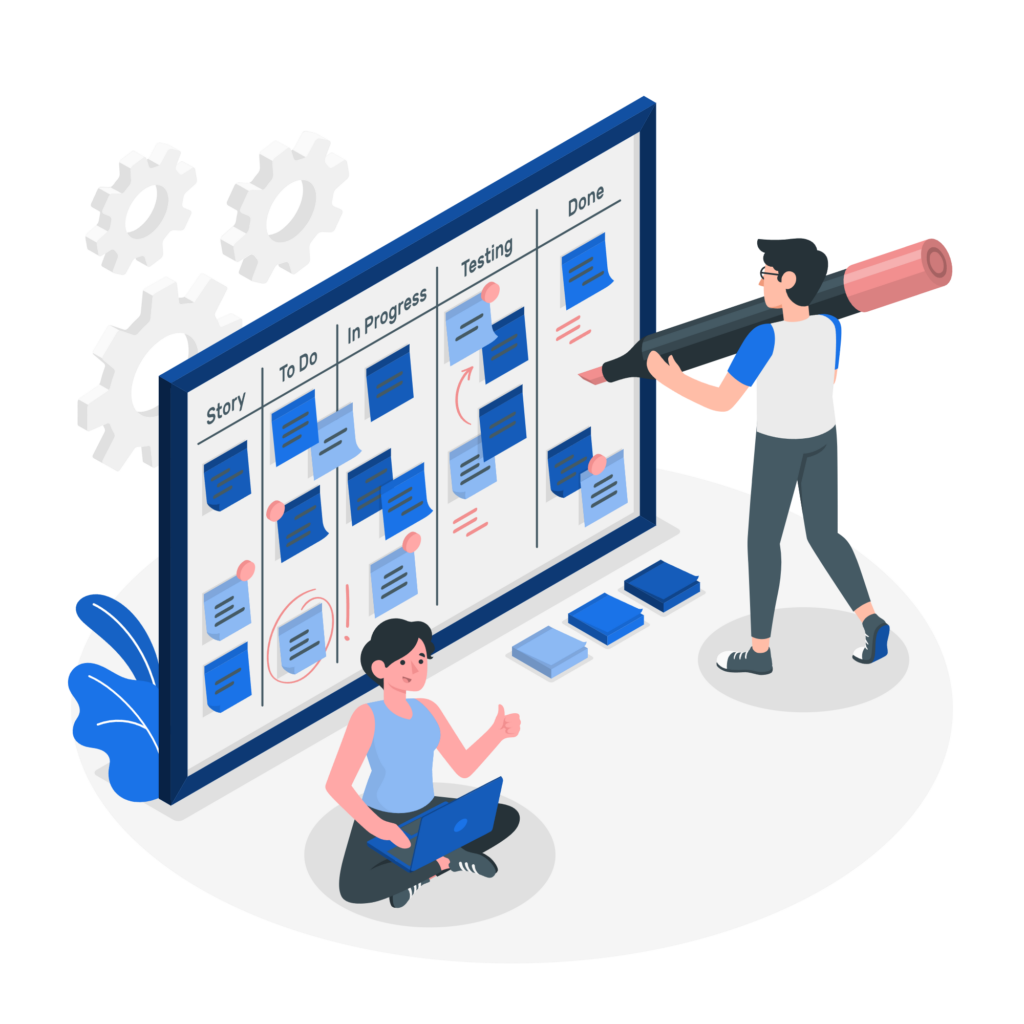
- Allocate sufficient budget for ongoing maintenance, repairs, and replacements based on the expected lifespans of assets.
- Consider long-term financial planning to ensure the availability of funds when assets need replacement.
Regular Audits and Assessments:
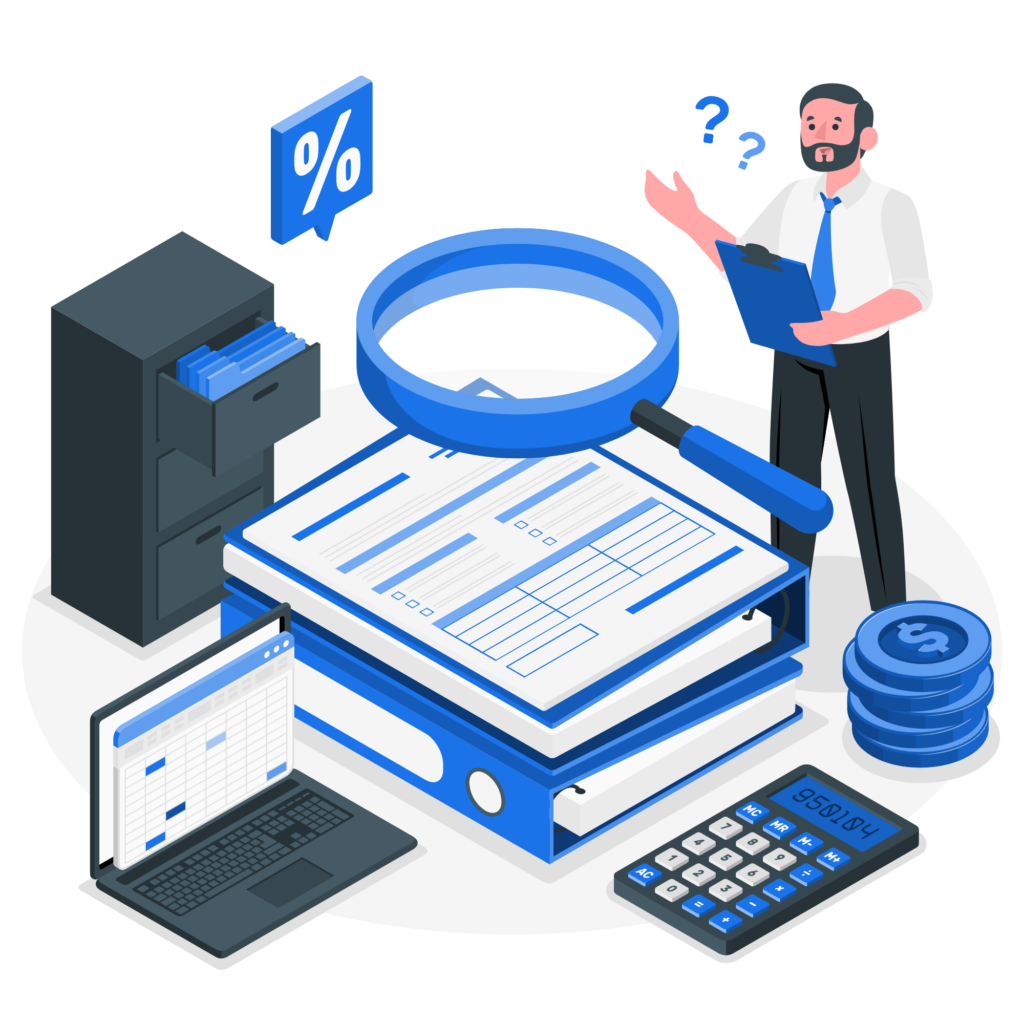
- Conduct periodic audits and assessments of your asset management practices to identify areas for improvement and ensure compliance with established strategies.
By following these steps, you can increase the expected life of assets across all your facilities, leading to better operational efficiency, reduced downtime, and optimized use of resources.