Introduction:
Effective equipment lifecycle management is essential for facilities maintenance to ensure optimal performance, minimize downtime, and control costs. However, navigating the complexities of equipment lifecycle management can be challenging for facility managers. In this blog post, we’ll explore the key components of equipment lifecycle management, common challenges faced by facility managers, and strategies to overcome them.
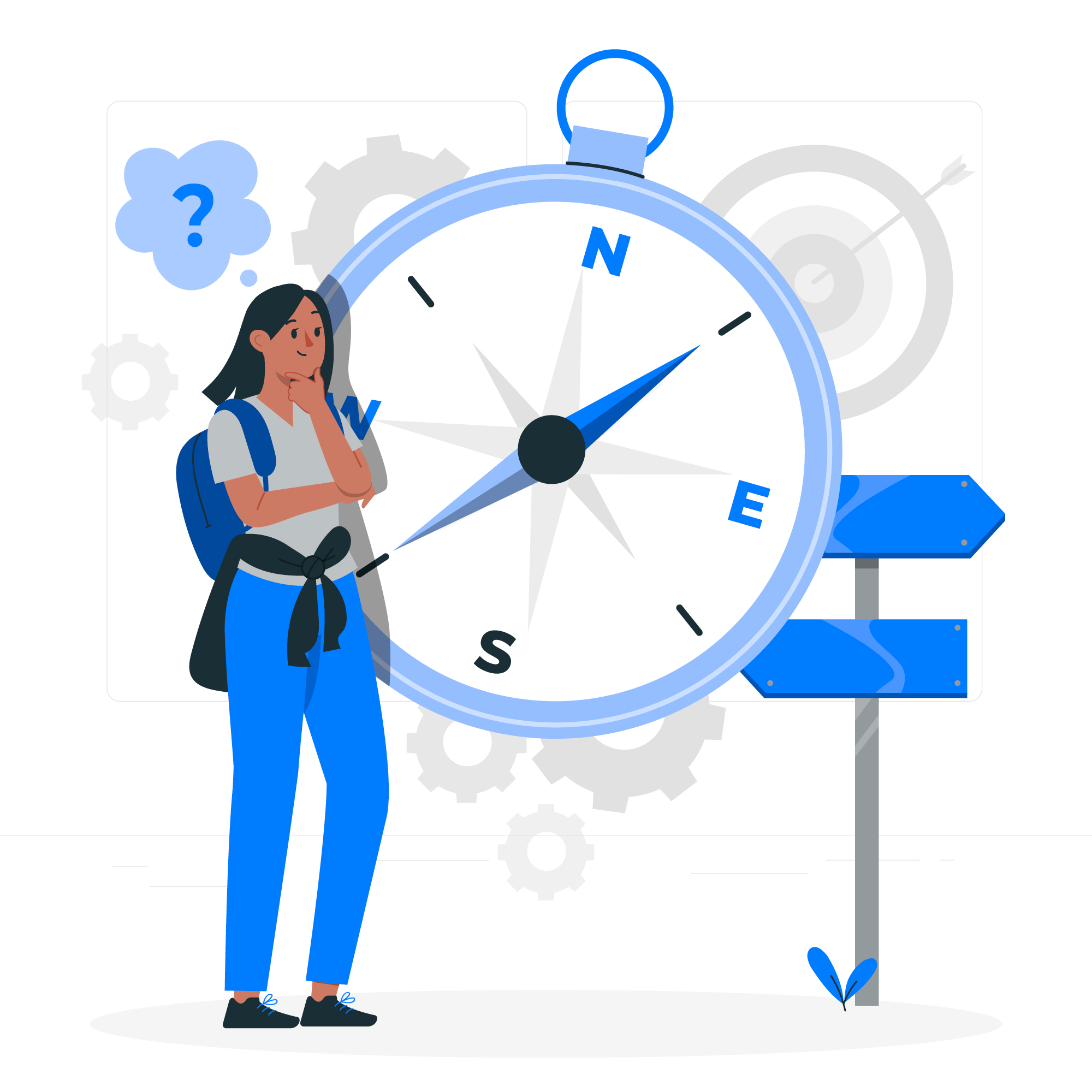
Understanding Equipment Lifecycle Management:
Equipment lifecycle management involves the strategic planning, acquisition, operation, maintenance, and disposal of assets throughout their lifecycle. It encompasses various stages, including:
Acquisition: The process of selecting and purchasing equipment that meets the facility’s needs and specifications.
Installation: Proper installation and commissioning of equipment to ensure functionality and safety.
Operation: Regular operation and monitoring of equipment to maintain performance and productivity.
Maintenance: Scheduled maintenance activities to prevent breakdowns, extend equipment lifespan, and optimize performance.
Upgrades and Repairs: Implementing upgrades and repairs as needed to keep equipment up-to-date and in good working condition.
Decommissioning and Disposal: Proper disposal or decommissioning of equipment at the end of its useful life, including recycling or environmentally responsible disposal methods.
Challenges in Equipment Lifecycle Management:
Facility managers face several challenges in managing the lifecycle of equipment effectively:
Lack of Visibility: Limited visibility into equipment inventory, condition, and maintenance history can make it difficult to make informed decisions about maintenance and replacement.
Budget Constraints: Limited budgets may restrict investments in new equipment, upgrades, or proactive maintenance, leading to increased risk of equipment failure and downtime.
Aging Infrastructure: Aging infrastructure can pose reliability and performance issues, requiring more frequent maintenance and repairs to keep equipment operational.
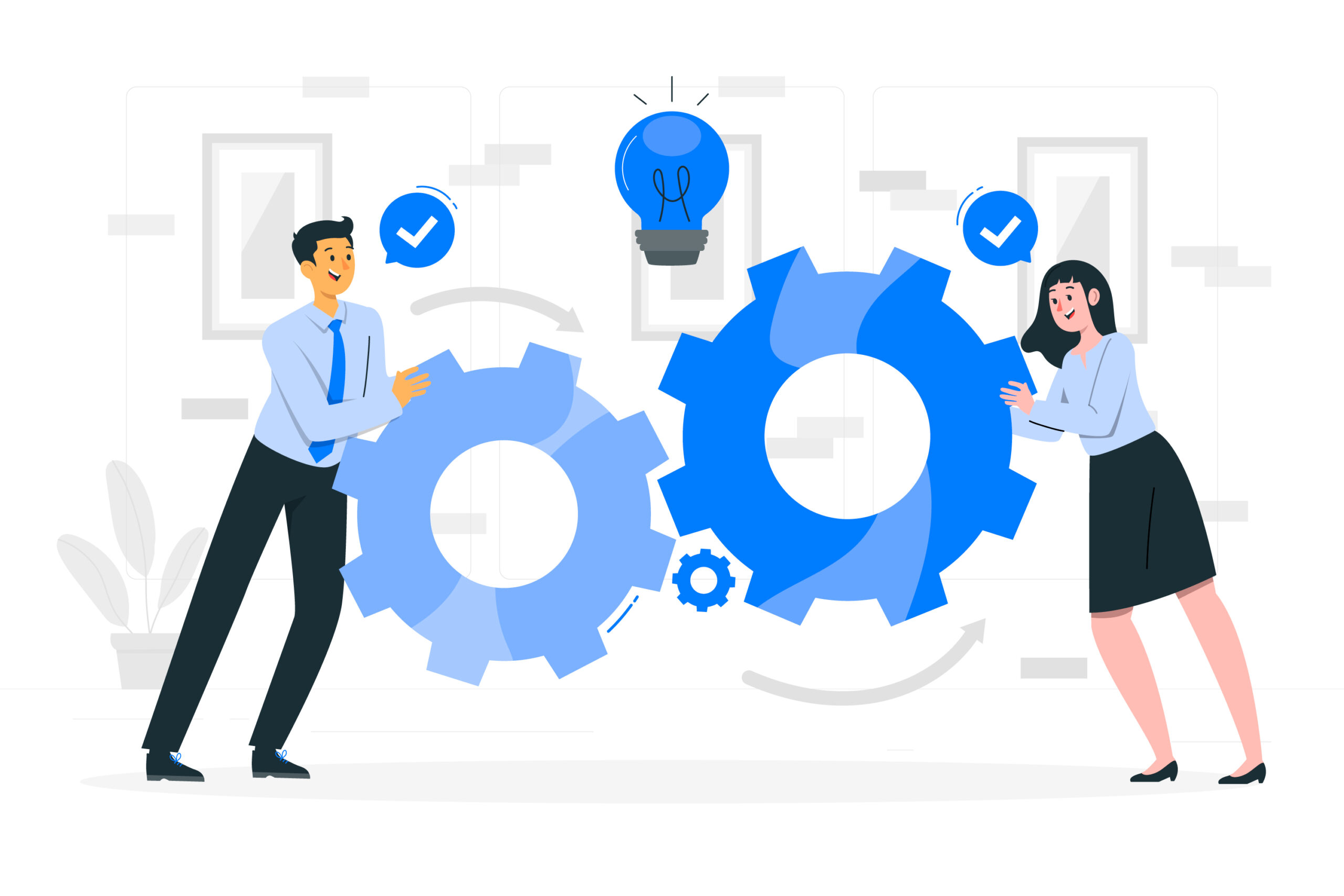
Technological Obsolescence: Rapid advancements in technology can render equipment obsolete, making it challenging to keep up-to-date with the latest innovations and standards.
Compliance and Regulations: Meeting regulatory requirements and ensuring compliance with safety and environmental standards adds complexity to equipment lifecycle management.
Strategies for Effective Equipment Lifecycle Management:
To overcome these challenges and optimize equipment lifecycle management, facility managers can implement the following strategies:
Asset Tracking and Management Systems: Utilize asset tracking software and management systems to maintain accurate records of equipment inventory, maintenance history, and lifecycle data.
Predictive Maintenance: Implement predictive maintenance techniques, such as condition monitoring and predictive analytics, to identify potential equipment failures before they occur and schedule maintenance proactively.
Lifecycle Cost Analysis: Conduct lifecycle cost analysis to evaluate the total cost of ownership of equipment, including acquisition, operation, maintenance, and disposal costs, to make informed decisions about investments and replacements.
Regular Inspections and Audits: Conduct regular inspections and audits of equipment to assess its condition, identify maintenance needs, and prioritize repairs or replacements.
Strategic Planning and Budgeting: Develop a comprehensive equipment lifecycle management plan that aligns with organizational goals and objectives, including budgeting for maintenance, upgrades, and replacements over the equipment’s lifespan.
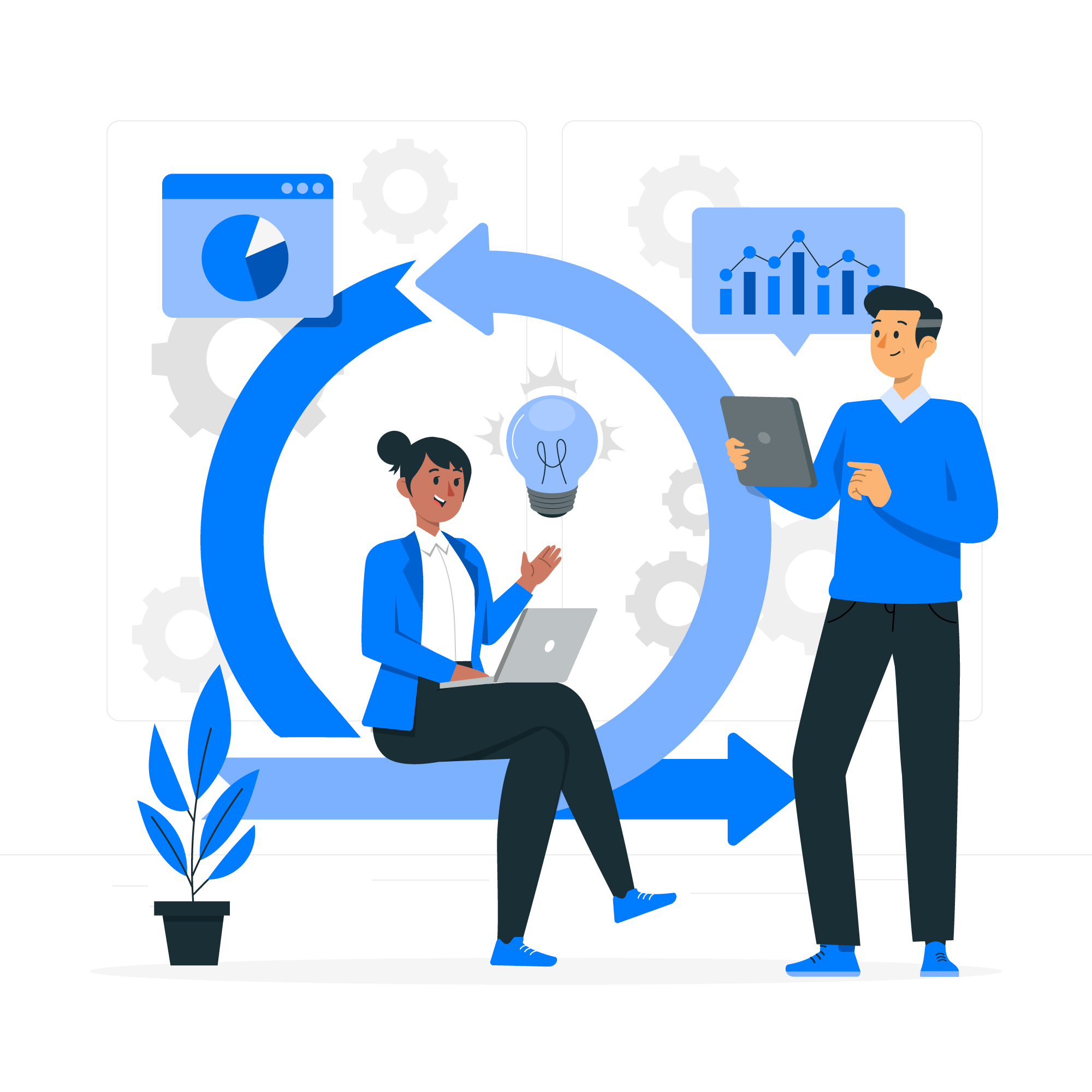
Conclusion:
Effectively managing the lifecycle of equipment in facilities maintenance requires careful planning, proactive maintenance, and strategic decision-making. By addressing challenges such as lack of visibility, budget constraints, aging infrastructure, technological obsolescence, and compliance requirements, facility managers can optimize equipment performance, minimize downtime, and control costs throughout the lifecycle. By implementing asset tracking systems, predictive maintenance techniques, lifecycle cost analysis, regular inspections, and strategic planning, facilities can navigate the complexities of equipment lifecycle management more effectively and ensure the long-term reliability and efficiency of their assets.